Schleifbrand ist eine thermisch bedingte Schädigung der geschliffenen Werkstückrandzonen und entsteht, wenn beim Schleifen eine zu große Wärmeentwicklung auftritt. Dies führt zu Anlasszonen, Neuhärtezonen bis hin zu Rissen, mit veränderter Härte und reduzierter Druckeigenspannung oder sogar Zugeigenspannung. Das Auftreten von Schleifbrand beeinträchtigt die Qualität der bearbeiteten Werkstücke durch erhebliche Reduktion der Ermüdungsfestigkeit. Daher gehört die Untersuchung auf Brandmarken zu den am häufigsten durchgeführten Prüfungen nach der Bearbeitung. Ziel des Vorhabens ist die Qualitätsverbesserung und -sicherung von Schleifprozessen durch den Einsatz einer kombinierten optischen und elektromagnetischen Sensortechnologie und die Analyse der Prozessdaten in einer Cloud. So ensteht ein intelligentes selbstlernen-des Regelsystem zur optimalen Wahl von Schleifparametern mit dem Ziel einer möglichst hohen Abtragsrate bei gleichzeitig zuverlässigen und beherrschten Prozessbedingungen.

links: Schematische Darstellung des geplanten mikrotechnisch hergestellten Spulen Arrays (MEMS). Typ. Größe einer Spule wird bei 150×150 μm² liegen, ein Gesamtarray (10×10) damit bei ca.9 mm². Auch größere Flächen zur Abdeckung ganzer Werkstückbereiche sind möglich. rechts: eine in unserem Labor (HFU) mittels Elektroplating abgeformte, ca 200 μm dicke ferromagnetische NiCo-Schicht. Zur Erzeugung der senkrechten Strukturkanten wird eine mittels DRIE tiefgeätzte Si-Vorform galvanisch abgeformt. [Quelle: Institut für Mikrosystemtechnik (iMST), Hochschule Furtwangen]
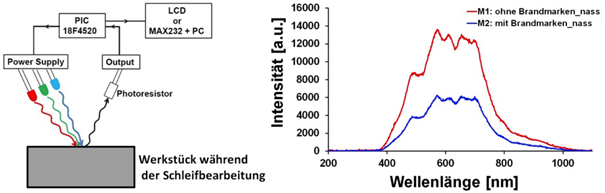
Konzept eines faseroptischen Brandmarkenerkennungssensors. Mit unterschiedlichen Wellenlängen werden Referenzierungen zur Unterdrückung von Störsignalen in rauer Umgebung vorgenommen, ausgewertet wird das vom Werkstück rückreflektierte Licht, rechts: gemessenes Spektrum von Brandmarken (mit Wasser bedeckt), [Quelle: Institut für Mikrosystemtechnik (iMST), Hochschule Furtwangen]